Principal Investigator(s):
Hyonny Kim
Summary:
Impact damage to laminated composite aircraft structures, when subjected to in-flight impact by hailstones, can be extensive internally while exhibiting low external visual detectability. Basic research studies have established methods for determining minimum aircraft skin thickness to be resistant from hailstone impacts. Fundamental study of ice behavior and properties enabled establishment of finite element based modeling simulation which accurately represents the ice during impact.
Conventional methods for evaluating blast loads on structures require the use of explosives and remote test facilities. Although detonating charges provides the most realistic test conditions for understanding blast effects, non-explosive techniques such as shock tubes and gas guns are popular alternatives to recreate (simulate) blast events in a safe, controlled lab environment. Some advantages include repeatable, consistent application of loads, no fire and debris cloud obscuring high speed camera observation, and limited shockwaves which can damage sensors and equipment. Generally, these non-explosive methods test smaller specimens and/or produce limited impulse levels. This research activity has developed a non-explosive methodology for applying representative blast loads onto large-sized (e.g., 610 x 610 mm or greater) flexible composite panels using fast (25 m/s) servo- hydraulic actuators tuned to match the specific impulse of an equivalent explosive charge. Control of the applied impulse loading and time-dependent characteristics of the pulse are controlled using “pulse-shaping” techniques and spatial-tuning of the impact mass distribution.
Vehicle Armor Blast Response

Principal Investigator(s):
H. Alicia Kim
Researcher(s):
Sandiliya Kambampati
Summary:
We developed a level set topology optimization method for 3D cooling channels, considering convective heat transfer for high Reynolds number flows. The Darcy potential flow is used to simulate the flow using the finite element method. The resulting velocity field is used in a convection-diffusion model to simulate the heat transfer using the finite element method. The pressure drop and the average temperature are considered as the objectives, which are minimized subject to a volume constraint and a maximum length scale constraint. Our results show that the pressure drop and the average temperature are conflicting criteria. We show an example in 3D where we optimize the cooling channel topology that conforms to the surface of a sphere.
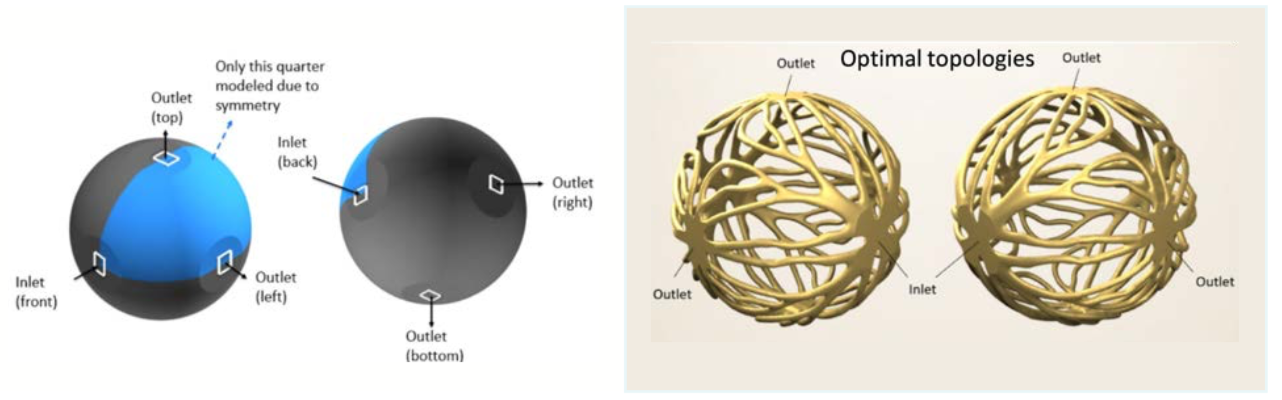
Principal Investigator(s):
Yu Qiao
Summary:
Stress wave mitigation in porous materials, such as silica monoliths and PTFE foams, are investigated. As shown in Figure 1, a hat-shaped setup on the SHPB testing system is used to induce force on the porous silica monoliths with different average pore sizes, from a few nanometers to a few hundreds of microns. Under the same shear rate and the same shear displacement, if the pore size is as large as 100 microns, the local softening caused by cell collapse will promote the formation of shear banding along the direction of shear force, and the influence area encircled by orange line will be localized. Whereas if the pore size is small enough like tens of nanometers, local hardening ahead of the shear banding will happen, leading a large influence area and thus more energy will be absorbed by the porous materials.
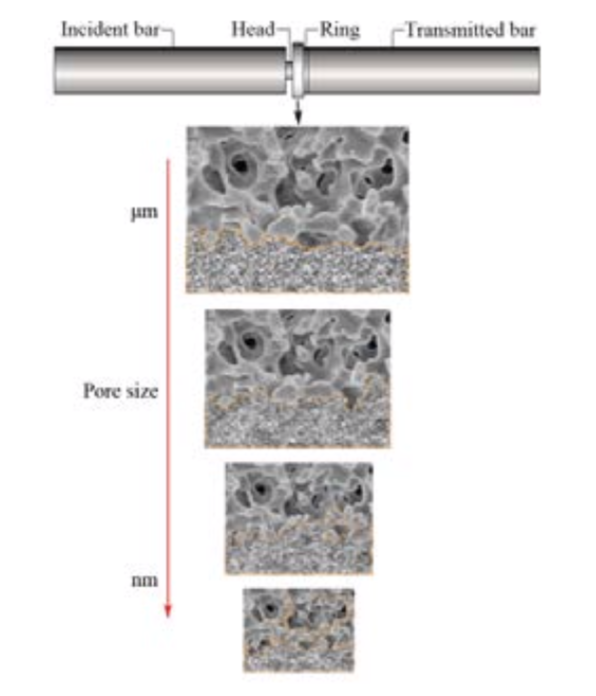
Principal Investigator(s):
Ken Loh
Researcher(s):
Yujin Park
Summary:
Many of nature’s creations, such as octopus and cuttlefish, can alter their skin properties to adapt and camouflage to their surroundings. Inspired by these biological systems, the Active, Responsive, Multifunctional, and Ordered-materials Research (ARMOR) Lab has designed Active Skins that can dynamically and reversibly morph their surface texture in a controlled manner. The objective of this project is to design skin-like structures that can shapeshift and alter their surface texture for camouflage. By designing the unit cell pattern of these flexible, 3D-printed, and planar structures, these Active Skins exhibit 2D to 3D deformations when tension is applied. In addition, the direction of these induced out-of-plane deformations can be reliably controlled by introducing instabilities or notches at selective locations in the structure. To harness these designs for specific functionalities, large arrays of these Active Skin unit cells have been fabricated. Each unit cell within the array can include, omit, or vary the placement of notch imperfections to elicit a specific out-of-plane deformation response. When assembled into an array, these Active Skins can function as a large- area gripper or be actuated to reveal an embedded “1 2 3” pattern, thus demonstrating the first concept of a dynamically variable camouflage system.
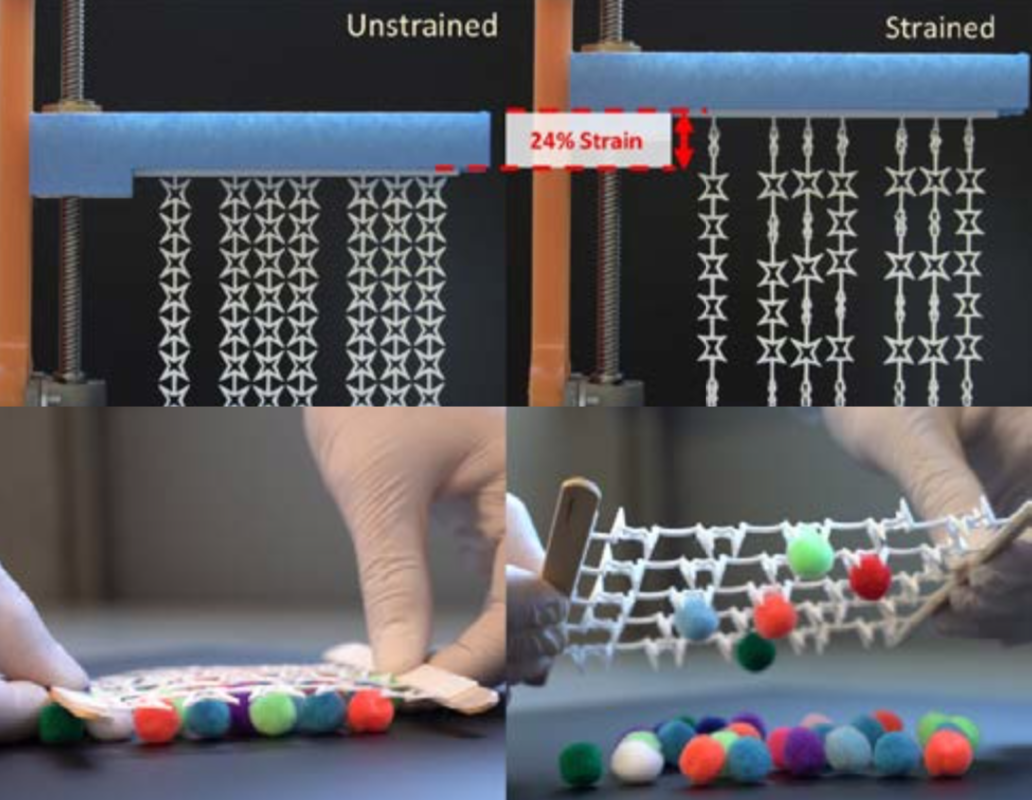
Principal Investigator(s):
Ken Loh
Researcher(s):
Yun-an Lin
Summary:
Wearable sensors have attracted considerable interest among the general public due to increased awareness in personal health and wellness management. In particular, wearable sensors that can capture the detailed movements and strains of muscles can facilitate a holistic assessment of muscle movement, performance, and precursors of musculoskeletal injuries. The objective of this Office of Naval Research project is to develop a multifunctional wearable sensing platform for warfighter performance monitoring. The Active, Responsive, Multifunctional, and Ordered-materials Research (ARMOR) Lab has designed “Smart K-Tape” sensors by integrating strain-sensitive nanocomposites with commercially available kinesiology tape. K-tape is a self-adhering, stretchable, fabric-based tape affixed onto the skin for supporting muscles and joints, as well as for relieving pain and swelling. The incorporation of printed graphene-based thin films with K-tape enables the measurement of distributed strains as the warfighter (or athlete) undergoes different training and field exercises. Laboratory tests have shown that these Smart K-Tape sensors exhibit 15 to 100 times greater sensitivities than foil-based strain gages while exhibiting repeatable and high signal-to-noise ratio response. Human subject pilot testing has confirmed that these sensors are capable of measuring muscle and joint movements as individuals perform different types of motions. This project involves close collaborations with the Naval Health Research Center in Point Loma and the Naval Medical Center San Diego. The long-term goal is to deploy these sensors for warfighter performance and physiological monitoring while acquiring the data streams necessary for assembling a personalized Digital Twin for each warfighter.
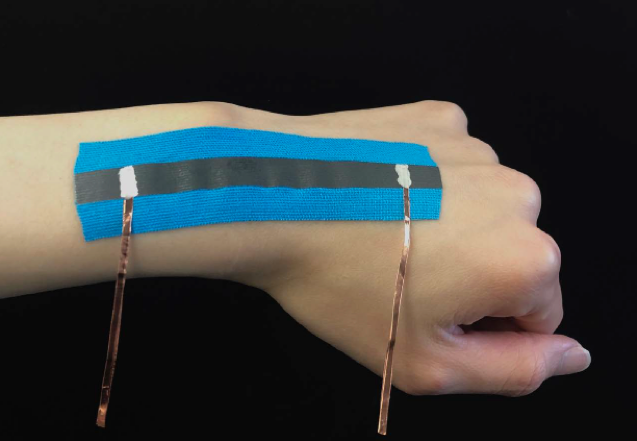
Principal Investigator(s):
Michael Todd
Summary:
Ultrasonic-guided wave interrogation using piezoelectric arrays and full-field laser ultrasonic inspection has evolved into a very active research area. This research focuses on the detection, classification, and prognosis of damage using elastic waves as the interrogation mechanism. The novel approach in this work is the embedding of stochastic models and parametric curve scanning methods to account for the uncertainty of model/physical parameters, in order to derive an optimal detection process that supports predictive modeling with quantified uncertainty. Research is focusing on maximum likelihood estimates for detecting and localizing small scatterers in complex aerospace composite and metallic structures. Detection is accomplished using generalized likelihood testing, probabilistic imaging methodologies, and optimized data domain transformations.
Principal Investigator(s):
Shabnam J. Semnani
Summary:
Microstructure of complex synthetic and natural materials (e.g. fiber composites, cementitious materials, and geomaterials) determines their overall properties and performance in engineering applications. We develop advanced techniques to incorporate the effects of microstructure of materials into computational models using machine learning and experimental material characterization techniques. The goal of this work is to enable fast and accurate simulations of engineering systems made of complex materials and to develop advanced tools for efficient material discovery and design.
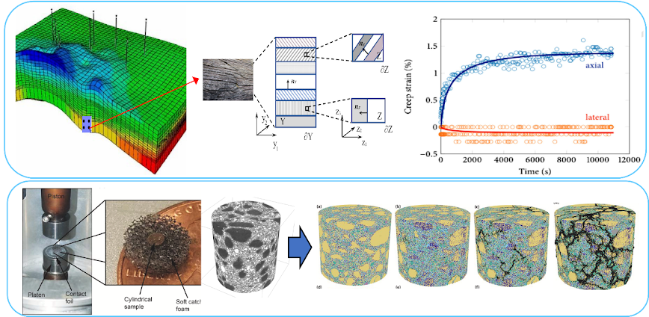